NDT Ultrasonic Testing adalah salah satu metode pengujian non-destruktif (Non-Destructive Testing) yang digunakan untuk mendeteksi cacat atau ketidaksempurnaan di dalam material tanpa merusaknya. Metode ini menggunakan gelombang ultrasonik berfrekuensi tinggi yang dipancarkan ke dalam material untuk menganalisis struktur internal, ketebalan, serta potensi keretakan atau rongga tersembunyi. Karena kemampuannya yang akurat dan efisien, teknik ini sering diterapkan di berbagai sektor industri seperti manufaktur, konstruksi, perminyakan, dan penerbangan.
Kelebihan dan Kekurangan Ultrasonic Testing
Seperti halnya metode pengujian lainnya, ultrasonic testing memiliki keunggulan dan keterbatasan. Memahami kelebihan dan kekurangannya sangat penting untuk menentukan kapan dan di mana metode ini paling tepat digunakan dalam proses inspeksi material.
—
Kelebihan Ultrasonic Testing
Salah satu keunggulan utama dari ultrasonic testing adalah tingkat akurasi yang tinggi dalam mendeteksi cacat internal. Teknik ini mampu mengidentifikasi retakan kecil, porositas, atau ketidaksempurnaan lain yang tidak dapat dideteksi oleh metode visual atau permukaan. Dengan memanfaatkan gelombang ultrasonik, pengujian ini dapat memberikan informasi detail tentang lokasi dan ukuran cacat secara presisi.
Keunggulan lainnya adalah kemampuannya untuk menembus material dengan ketebalan yang bervariasi. Hal ini menjadikan ultrasonic testing sangat berguna dalam pengujian struktur besar atau komponen logam tebal, seperti pipa industri atau struktur baja. Teknologi ini juga memungkinkan akses hanya dari satu sisi permukaan, yang sangat membantu ketika sisi lain tidak dapat dijangkau.
Metode ini termasuk kategori pengujian non-destruktif, artinya tidak akan merusak benda kerja atau komponen yang diuji. Oleh karena itu, sangat ideal untuk komponen yang bernilai tinggi atau tidak bisa digantikan dengan mudah. Selain itu, data hasil pengujian dapat direkam dan dianalisis kembali, memberikan keunggulan dalam dokumentasi dan pelacakan kualitas produk secara historis.
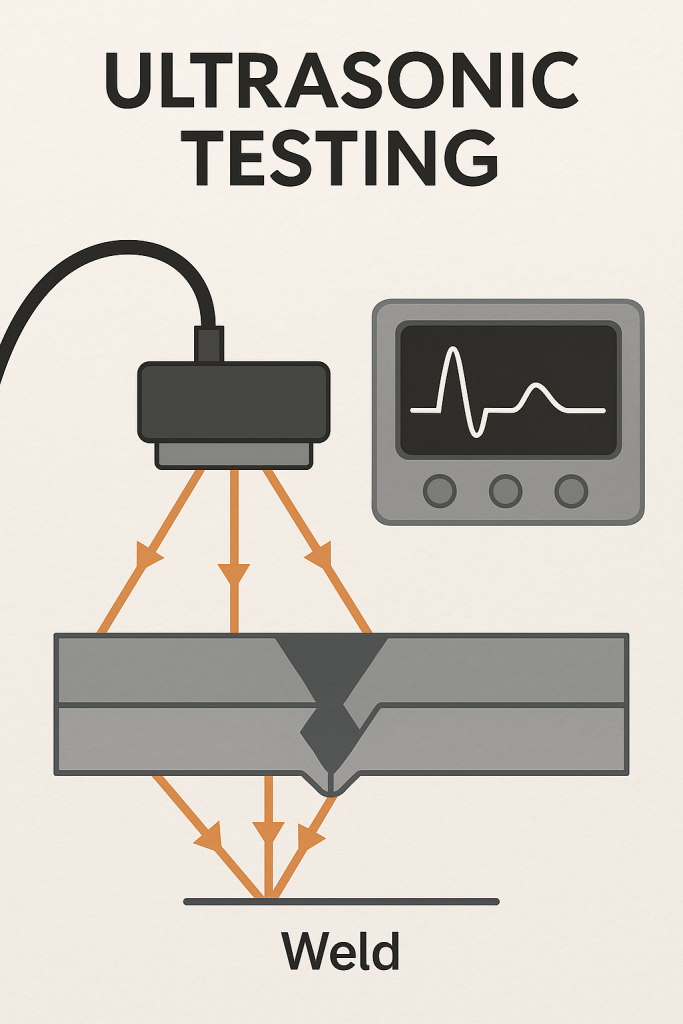
—
Kekurangan Ultrasonic Testing
Meskipun memiliki banyak kelebihan, ultrasonic testing juga memiliki keterbatasan yang perlu diperhatikan. Salah satunya adalah kebutuhan akan operator yang terlatih dan berpengalaman. Interpretasi sinyal pantulan ultrasonik memerlukan keahlian khusus agar hasilnya akurat. Kesalahan dalam membaca sinyal bisa menyebabkan cacat tidak terdeteksi atau justru memicu kesalahan diagnosis.
Permukaan benda uji juga harus dipersiapkan dengan baik. Ultrasonic testing membutuhkan kontak langsung dengan permukaan melalui couplant, yaitu zat perantara seperti gel atau air, agar gelombang bisa masuk ke dalam material. Jika permukaan kotor, kasar, atau tidak rata, hasil pengujian bisa terganggu atau bahkan tidak terbaca.
Metode ini juga memiliki keterbatasan pada material dengan bentuk kompleks atau geometri yang rumit. Komponen dengan sudut tajam, rongga sempit, atau bentuk melengkung sering kali menyulitkan penempatan transduser dan pembacaan gelombang pantulan. Dalam kasus seperti ini, metode pengujian lain mungkin lebih efektif.
Fungsi Ultrasonic Test
Ultrasonic test memiliki berbagai fungsi penting dalam dunia industri, terutama dalam menjaga integritas dan kualitas material. Dengan kemampuan mendeteksi cacat internal secara akurat tanpa merusak objek uji, metode ini menjadi salah satu teknik NDT yang paling diandalkan dalam inspeksi struktural dan pemeliharaan berkala.
—
Deteksi Cacat Internal
Salah satu fungsi utama dari ultrasonic test adalah mendeteksi cacat yang tersembunyi di dalam material. Cacat seperti retakan, rongga, porositas, atau delaminasi dapat mengganggu kekuatan dan keandalan struktur, terutama pada komponen yang menerima beban besar atau bekerja dalam kondisi ekstrem.
Gelombang ultrasonik akan dipantulkan oleh batas antar material atau perubahan densitas. Ketika terjadi pantulan yang tidak normal, operator dapat mengidentifikasi keberadaan cacat dengan menganalisis sinyal pantulan. Dengan teknik ini, potensi kerusakan dapat ditemukan lebih awal sebelum menyebabkan kegagalan fungsi.
Contoh Laporan Deteksi Cacat Internal dengan Ultrasonic Testing PDF
—
Pengukuran Ketebalan Material
Ultrasonic testing juga digunakan untuk mengukur ketebalan material secara akurat, bahkan dari satu sisi permukaan saja. Fungsi ini sangat berguna dalam industri seperti perminyakan dan kelautan, di mana korosi dinding pipa atau tangki penyimpanan harus dipantau secara berkala.
Pengukuran ketebalan dilakukan dengan menghitung waktu tempuh gelombang ultrasonik dari transduser menuju permukaan dalam dan kembali. Dari data tersebut, sistem dapat menghitung ketebalan aktual material, bahkan dengan akurasi hingga satuan milimeter.
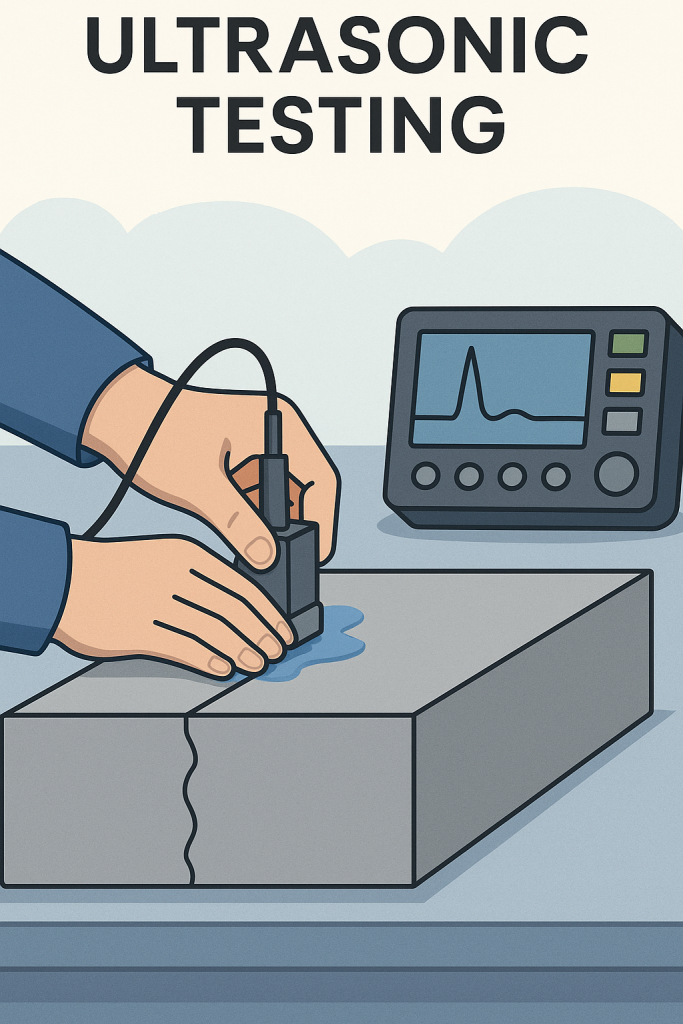
—
Verifikasi Struktur Las atau Sambungan
Dalam pengujian sambungan las, ultrasonic test berperan penting dalam memverifikasi kualitas penyambungan logam. Cacat seperti incomplete fusion, lack of penetration, atau retakan mikro yang tidak terlihat secara visual dapat dideteksi melalui metode ini.
Penerapan ultrasonic test pada sambungan las memberikan keuntungan karena mampu menilai integritas sambungan tanpa perlu membongkar atau memotong struktur. Hasil pengujian juga bisa digunakan sebagai dokumen pendukung untuk memenuhi standar kualitas internasional.
—
Kontrol Kualitas dan Keamanan Produk
Ultrasonic test menjadi bagian penting dari sistem kontrol kualitas dalam proses produksi. Dengan memastikan bahwa setiap komponen bebas dari cacat internal, perusahaan dapat menjamin produk yang dikirim ke pelanggan aman dan sesuai spesifikasi teknis.
Di sektor-sektor dengan tingkat risiko tinggi seperti penerbangan, energi nuklir, atau konstruksi jembatan, metode ini menjadi bagian tak terpisahkan dari proses quality assurance. Keandalan produk dan keselamatan pengguna akhir dapat dipastikan melalui inspeksi ultrasonic secara berkala.
Ultrasonic Test Welding
Pengujian ultrasonic sangat umum digunakan dalam inspeksi sambungan las, terutama pada struktur yang membutuhkan tingkat keselamatan tinggi. Dengan metode ini, kualitas pengelasan dapat dinilai secara menyeluruh tanpa merusak komponen, menjadikannya pilihan ideal dalam industri konstruksi, energi, dan manufaktur berat.
—
Penerapan pada Sambungan Las
Ultrasonic test diterapkan pada sambungan las untuk mengevaluasi integritas dan kesesuaian hasil lasan dengan standar teknis yang ditetapkan. Metode ini sangat efektif mendeteksi cacat di sepanjang area las yang tidak dapat dijangkau oleh pengujian visual biasa.
Dengan menempatkan transduser di sepanjang sambungan, gelombang ultrasonik dapat memetakan struktur dalam lasan. Pantulan yang tidak normal menunjukkan adanya cacat seperti retakan, undercut, atau incomplete fusion. Hasilnya bisa langsung dianalisis oleh teknisi terlatih menggunakan perangkat display atau software khusus.
Penerapan ultrasonic test pada sambungan las biasanya dilakukan sebagai bagian dari quality control pasca-pengelasan maupun selama inspeksi berkala pada struktur yang sudah digunakan.
—
Deteksi Cacat Seperti Porositas dan Retakan
Cacat seperti porositas, retakan mikro, atau slag inclusion merupakan potensi kerusakan serius dalam pengelasan. Cacat ini dapat menurunkan kekuatan struktural dan menyebabkan kegagalan pada kondisi kerja tertentu.
Ultrasonic test memiliki sensitivitas tinggi terhadap perubahan akustik dalam material. Ketika gelombang bertemu rongga kecil seperti pori atau retakan, sinyal akan terdistorsi atau terpantul kembali dengan pola khusus. Inilah yang kemudian dianalisis untuk mengetahui jenis dan ukuran cacat.
Deteksi ini sangat penting pada proyek-proyek kritis, seperti pengelasan pipa tekanan tinggi, struktur jembatan, dan bejana tekan. Dengan pengujian ultrasonic, risiko kegagalan akibat cacat tersembunyi bisa diminimalkan sejak awal.
—
Evaluasi Kualitas Hasil Pengelasan
Selain mendeteksi cacat, ultrasonic test juga digunakan untuk mengevaluasi secara keseluruhan kualitas hasil pengelasan. Ini mencakup pemantauan konsistensi sambungan, kedalaman penetrasi las, serta distribusi panas yang merata.
Teknik ini memberikan informasi kuantitatif dan kualitatif mengenai kekuatan sambungan. Dengan data tersebut, tim inspeksi dapat mengambil keputusan teknis apakah sambungan tersebut memenuhi standar atau perlu dilakukan perbaikan (repair welding).
Evaluasi ini sangat berguna dalam pengujian struktur berskala besar di mana ribuan sambungan las perlu diuji secara efisien dan akurat.
—
Standar Pengujian Las Menggunakan UT
Pengujian las dengan ultrasonic testing dilakukan mengikuti standar internasional seperti ASME, AWS D1.1, atau ISO 17640. Standar ini mengatur prosedur pelaksanaan, jenis cacat yang harus dideteksi, dan kriteria penerimaan berdasarkan ukuran, posisi, serta dampaknya terhadap struktur.
Adanya standar ini memastikan bahwa proses pengujian dilakukan secara konsisten dan hasilnya dapat dipercaya oleh semua pihak yang terlibat dalam proyek. Selain itu, standar juga menjadi acuan dalam pelatihan dan sertifikasi personel UT agar mereka memiliki kompetensi teknis yang dibutuhkan.
Penerapan standar dalam UT welding menjamin kualitas dan keselamatan komponen las dalam jangka panjang, terutama pada infrastruktur vital dan industri berisiko tinggi.
Alat Ultrasonic Test
Alat ultrasonic test adalah perangkat utama dalam metode Non-Destructive Testing berbasis gelombang suara berfrekuensi tinggi. Alat ini dirancang untuk mengirim dan menerima gelombang ultrasonik ke dalam material guna mendeteksi cacat internal, mengukur ketebalan, atau memverifikasi struktur sambungan. Peralatan ini hadir dalam berbagai bentuk dan konfigurasi, tergantung pada jenis pengujian yang dilakukan.
—
Transduser (Probe)
Transduser atau probe adalah komponen penting yang berfungsi mengubah energi listrik menjadi gelombang ultrasonik dan sebaliknya. Terdapat berbagai jenis transduser, antara lain straight beam, angle beam, dan dual element, yang masing-masing memiliki fungsi spesifik dalam pengujian.
Straight beam digunakan untuk inspeksi umum dan pengukuran ketebalan. Sementara itu, angle beam sering dipakai dalam pengujian sambungan las karena mampu mendeteksi cacat yang terletak pada sudut tertentu. Dual element memiliki dua kristal yang memisahkan fungsi pengiriman dan penerimaan, memberikan hasil yang lebih jelas pada permukaan kasar atau tidak rata.
Pemilihan jenis transduser yang tepat sangat mempengaruhi keakuratan hasil pengujian, sehingga harus disesuaikan dengan jenis material dan bentuk objek yang diperiksa.
—
Flaw Detector
Flaw detector adalah perangkat elektronik utama yang memproses sinyal dari transduser. Alat ini menampilkan hasil gelombang pantulan dalam bentuk grafik (biasanya A-scan), yang kemudian dianalisis oleh teknisi untuk menentukan keberadaan, posisi, dan ukuran cacat.
Flaw detector modern dilengkapi dengan fitur digital, penyimpanan data, dan konektivitas ke komputer atau perangkat lunak analisis. Beberapa model bahkan memiliki kemampuan phased array atau TOFD (Time of Flight Diffraction) untuk pemetaan cacat yang lebih kompleks.
Ketepatan flaw detector sangat menentukan kualitas interpretasi hasil UT. Oleh karena itu, kalibrasi rutin dan pemahaman yang mendalam terhadap sistem pembacaan sangat dibutuhkan.
—
Couplant
Couplant adalah bahan antara (biasanya berupa gel atau cairan) yang digunakan untuk memastikan transmisi gelombang ultrasonik dari transduser ke permukaan material tanpa gangguan udara. Tanpa couplant, gelombang tidak akan masuk dengan baik ke dalam material sehingga hasil pengujian menjadi tidak akurat.
Jenis couplant yang digunakan tergantung pada kondisi lingkungan dan permukaan objek. Di lingkungan suhu tinggi, digunakan couplant khusus tahan panas. Pada permukaan halus atau datar, couplant berbasis air atau gel biasa sudah mencukupi.
Pemakaian couplant harus merata dan bebas gelembung agar transmisi gelombang berjalan optimal. Penggunaan yang tidak tepat bisa menyebabkan noise atau hilangnya sinyal pantulan yang penting.
—
Scanner atau Manipulator
Untuk pengujian pada area luas atau sulit dijangkau, digunakan alat bantu seperti scanner atau manipulator. Perangkat ini membantu menggerakkan transduser secara presisi dan konsisten di atas permukaan objek uji.
Beberapa scanner dilengkapi dengan motor dan sensor posisi, sehingga data yang dikumpulkan bisa dipetakan dalam bentuk gambar dua atau tiga dimensi. Ini sangat berguna pada inspeksi struktur kompleks seperti pipa besar, tangki, atau sayap pesawat.
Penggunaan scanner mempercepat proses pengujian dan meningkatkan konsistensi hasil, terutama dalam proyek-proyek berskala besar yang membutuhkan dokumentasi menyeluruh.
Prosedur Ultrasonic Testing
Prosedur Ultrasonic Testing (UT) adalah serangkaian langkah sistematis yang dilakukan untuk mendeteksi cacat atau ketidaksempurnaan di dalam material padat (seperti logam) dengan menggunakan gelombang ultrasonik berfrekuensi tinggi, tanpa merusak benda uji.
Prosedur ultrasonic testing mencakup serangkaian langkah sistematis yang harus dilakukan untuk mendapatkan hasil pengujian yang akurat dan dapat dipertanggungjawabkan. Prosedur ini umumnya mengikuti standar internasional dan memerlukan teknisi bersertifikasi agar pengujian dilakukan secara profesional dan konsisten.
—
Persiapan Permukaan dan Peralatan
Sebelum pengujian dilakukan, permukaan benda uji harus dipersiapkan dengan baik. Permukaan yang kotor, berkarat, atau kasar dapat mengganggu transmisi gelombang ultrasonik. Oleh karena itu, pembersihan menyeluruh sering kali diperlukan, baik dengan pengamplasan, pelarut, maupun alat pembersih mekanik.
Di sisi lain, peralatan seperti flaw detector, transduser, dan couplant harus diperiksa dan dipastikan dalam kondisi baik. Kalibrasi alat juga menjadi bagian penting dalam tahap ini. Kalibrasi dilakukan dengan menggunakan blok referensi standar untuk menyesuaikan sensitivitas dan ketepatan pengukuran alat.
Tahap persiapan menentukan keberhasilan keseluruhan proses UT. Jika diabaikan, hasil pengujian dapat menyimpang atau bahkan tidak valid.
—
Kalibrasi Instrumen
Kalibrasi dilakukan untuk memastikan bahwa alat mampu memberikan pembacaan yang akurat. Biasanya, teknisi menggunakan blok uji standar berbahan dan ketebalan tertentu yang telah ditentukan dalam prosedur atau standar yang digunakan.
Blok kalibrasi ini memiliki cacat buatan seperti lubang atau takikan yang digunakan untuk menguji kemampuan deteksi alat. Melalui kalibrasi, teknisi menyetel gain, range, dan parameter lainnya agar cocok dengan objek yang akan diuji.
Kalibrasi bukan hanya prosedur awal, tetapi juga dilakukan ulang secara berkala selama proses pengujian untuk menjamin konsistensi hasil. Hal ini terutama penting dalam proyek pengujian massal atau inspeksi jangka panjang.
—
Pelaksanaan Pengujian
Setelah alat dan permukaan siap, proses UT dapat dimulai. Transduser diletakkan pada permukaan benda uji dengan bantuan couplant untuk mengalirkan gelombang ultrasonik ke dalam material. Gelombang ini akan merambat dan memantul kembali jika menemui batas atau cacat internal.
Teknisi kemudian memantau sinyal pantulan melalui layar flaw detector. Pola sinyal atau pantulan abnormal menunjukkan kemungkinan adanya cacat seperti retakan, porositas, atau delaminasi. Posisi dan ukuran cacat dapat dihitung berdasarkan waktu pantulan dan amplitudo sinyal.
Pelaksanaan pengujian ini memerlukan keahlian teknis tinggi. Pengalaman teknisi sangat berpengaruh dalam membaca dan menafsirkan sinyal secara akurat.
—
Pencatatan dan Evaluasi Hasil
Setelah pengujian selesai, semua data harus dicatat secara rinci. Ini meliputi hasil pembacaan sinyal, lokasi cacat, ukuran, dan kedalamannya. Hasil tersebut dibandingkan dengan kriteria penerimaan sesuai standar yang digunakan, seperti ASME, ISO, atau AWS.
Jika hasil pengujian menunjukkan bahwa komponen berada di luar batas toleransi, maka tindakan perbaikan harus dilakukan, seperti pengelasan ulang atau penggantian bagian. Sebaliknya, jika hasil dalam batas aman, maka komponen dinyatakan lulus inspeksi.
Pencatatan yang baik juga penting sebagai dokumentasi teknis dan referensi jika terjadi kegagalan di kemudian hari. Evaluasi hasil biasanya dilakukan bersama oleh teknisi UT dan insinyur mutu untuk memastikan keputusan yang diambil tepat dan berdasar data.