Pengujian Non Destruktif atau Non-Destructive Testing (NDT) adalah teknik pemeriksaan material yang memungkinkan evaluasi tanpa harus merusak atau mengubah bentuk aslinya. Metode ini sangat penting dalam dunia industri karena dapat mendeteksi cacat atau ketidaksempurnaan pada suatu komponen tanpa harus memotong, melubangi, atau membongkarnya. NDT digunakan untuk menjamin keamanan, keandalan, dan kualitas suatu produk atau struktur tanpa mengganggu fungsi aslinya.
Pengertian Pengujian Non Destruktif (NDT)
Pengujian Non Destruktif merupakan metode inspeksi teknis yang dirancang untuk mengevaluasi karakteristik fisik dan integritas struktural dari material, komponen, atau sistem tanpa menyebabkan kerusakan. Teknik ini digunakan secara luas dalam berbagai sektor industri yang memerlukan pemeriksaan menyeluruh namun tetap menjaga kondisi asli benda uji.
Definisi NDT
Pengujian Non Destruktif (NDT) adalah pendekatan pemeriksaan teknis yang memungkinkan deteksi cacat atau anomali dalam material tanpa merusak struktur atau bentuk aslinya. Metode ini sangat berguna dalam memeriksa kualitas internal maupun eksternal dari suatu benda uji.
NDT dilakukan menggunakan berbagai teknologi seperti gelombang ultrasonik, medan magnet, sinar-X, dan cairan penetran, yang masing-masing memiliki keunggulan dalam mengidentifikasi jenis cacat tertentu. Teknik ini memungkinkan perusahaan untuk mempertahankan produk atau komponen dalam kondisi operasional selama proses inspeksi.
Perbedaan dengan Pengujian Destruktif (DT)
Pengujian Destruktif (DT) adalah metode yang melibatkan perusakan benda uji untuk mengetahui kekuatan, daya tahan, atau batas-batas teknis lainnya. Sementara itu, NDT tidak merusak dan dapat dilakukan berulang kali pada benda yang sama.
DT biasanya digunakan dalam pengujian laboratorium, di mana sampel dikompresi, ditarik, atau dibebani hingga gagal. Sebaliknya, NDT bisa diterapkan langsung di lapangan, bahkan saat komponen sedang beroperasi. Hal ini menjadikan NDT pilihan utama untuk pemeliharaan preventif dan inspeksi berkala.
Prinsip Dasar Pengujian NDT
Prinsip utama dalam NDT adalah mendeteksi ketidaksempurnaan atau perubahan sifat fisik material tanpa mengganggu bentuk dan fungsinya. Metode ini memanfaatkan perbedaan sifat material seperti densitas, konduktivitas, atau refleksi gelombang untuk mengidentifikasi cacat tersembunyi.
Setiap teknik NDT memiliki prinsip kerja unik, seperti pantulan gelombang pada Ultrasonic Testing atau gangguan medan magnet pada Magnetic Particle Testing. Keberhasilan metode ini bergantung pada pemilihan teknik yang sesuai, keterampilan operator, serta interpretasi hasil yang akurat.
Tujuan dan Manfaat Pengujian NDT
Pengujian Non Destruktif memiliki peran vital dalam berbagai sektor industri karena memungkinkan evaluasi material tanpa kerusakan. Tujuan utamanya adalah untuk menjaga keandalan, mencegah kegagalan komponen, serta menghemat biaya perbaikan dan penggantian. Dengan penerapan NDT yang tepat, perusahaan dapat meningkatkan keselamatan, efisiensi, dan mutu produksi.
Deteksi Cacat Material
Salah satu tujuan utama dari NDT adalah mendeteksi adanya cacat yang mungkin tersembunyi dalam material, baik pada permukaan maupun di bawah permukaan. Cacat tersebut bisa berupa retakan, porositas, rongga, delaminasi, atau diskontinuitas lainnya yang dapat mengganggu kekuatan dan integritas struktur.
Deteksi dini terhadap cacat sangat penting, terutama dalam industri yang mengutamakan keselamatan seperti penerbangan, energi nuklir, dan konstruksi. Dengan mendeteksi masalah sejak awal, risiko kerusakan serius dapat dihindari sebelum terjadi kegagalan fungsi.
Penjaminan Kualitas Produk
Pengujian NDT digunakan secara luas dalam proses kontrol kualitas untuk memastikan bahwa suatu produk atau komponen memenuhi standar spesifikasi teknis. Teknik ini memungkinkan pemeriksaan secara menyeluruh tanpa menghentikan produksi atau merusak hasil akhir.
Dalam praktiknya, NDT sering diterapkan pada tahap pasca-produksi untuk memverifikasi bahwa barang siap pakai tidak memiliki cacat tersembunyi yang dapat menimbulkan kerugian di kemudian hari. Hal ini mendukung proses sertifikasi dan meningkatkan reputasi produk di pasar.
Pencegahan Kegagalan Dini
NDT membantu mendeteksi potensi kegagalan sebelum komponen mengalami kerusakan yang parah atau berakibat fatal. Pencegahan ini penting untuk menghindari kecelakaan kerja, kerusakan alat berat, atau gangguan operasional yang dapat berdampak besar pada kelangsungan industri.
Dengan pemantauan berkala menggunakan NDT, peralatan dapat dipertahankan dalam kondisi optimal. Ini memberikan peluang bagi tim pemeliharaan untuk melakukan tindakan korektif sebelum kerusakan terjadi.
Efisiensi Biaya Perawatan dan Operasional
Penggunaan NDT dapat menurunkan biaya pemeliharaan karena kerusakan bisa diantisipasi sebelum berkembang menjadi masalah besar. Dengan begitu, waktu henti produksi dapat diminimalkan dan tidak diperlukan penggantian komponen secara menyeluruh.
Selain itu, pengujian yang tidak merusak memungkinkan komponen diuji berulang kali selama masa pakainya, tanpa menambah risiko keausan atau kerusakan tambahan. Ini menjadikan NDT sebagai solusi ekonomis yang mendukung program pemeliharaan prediktif dan berkelanjutan.
Metode Pengujian NDT
Pengujian Non Destruktif memiliki berbagai metode yang disesuaikan dengan jenis material, bentuk komponen, dan jenis cacat yang ingin dideteksi. Setiap metode memiliki prinsip kerja, keunggulan, dan keterbatasan tersendiri. Pemilihan metode yang tepat sangat menentukan akurasi dan efektivitas pemeriksaan.
Ultrasonic Testing (UT)
Ultrasonic Testing menggunakan gelombang suara berfrekuensi tinggi yang dipancarkan ke dalam material untuk mendeteksi cacat internal. Gelombang ini akan dipantulkan kembali jika menemui batas atau ketidaksesuaian dalam struktur material, seperti retakan atau rongga.
UT sangat efektif untuk mendeteksi cacat di bawah permukaan dan dapat digunakan pada berbagai jenis logam, termasuk baja dan aluminium. Metode ini cocok untuk pengujian komponen tebal, seperti pelat baja atau pipa industri. Kelebihan lainnya adalah kemampuannya memberikan data kuantitatif mengenai kedalaman dan ukuran cacat.
Namun, UT memerlukan permukaan kontak yang rata dan bersih, serta membutuhkan operator yang terlatih dalam menginterpretasikan hasil gelombang pantul. Penggunaan perangkat lunak dan peralatan digital telah membantu meningkatkan akurasi dan efisiensi metode ini.
Radiographic Testing (RT)
Radiographic Testing melibatkan penggunaan sinar-X atau sinar gamma untuk menembus material dan menangkap gambar bagian dalamnya pada film atau detektor digital. Cacat seperti porositas, retakan, atau inklusi dapat dikenali dari ketidakteraturan pada gambar radiograf.
Metode ini sangat berguna dalam mendeteksi cacat internal pada sambungan las, pengecoran logam, dan komponen dengan struktur kompleks. Salah satu keunggulan RT adalah kemampuan menghasilkan dokumentasi visual yang dapat disimpan dan dianalisis lebih lanjut.
Namun, RT memerlukan prosedur keselamatan radiasi yang ketat karena menggunakan sumber radiasi berbahaya. Selain itu, ketebalan material dan jenis logam dapat mempengaruhi kualitas gambar, sehingga pengaturan eksposur harus diperhitungkan secara cermat.
Magnetic Particle Testing (MT)
Magnetic Particle Testing digunakan untuk mendeteksi cacat permukaan dan dekat permukaan pada material ferromagnetik, seperti baja dan besi cor. Metode ini bekerja dengan memagnetisasi benda uji dan menaburkan partikel magnetik halus ke permukaan material.
Jika terdapat cacat, medan magnet akan bocor dan menarik partikel untuk berkumpul di sekitar area cacat, sehingga membentuk pola visual yang dapat dilihat langsung. MT sangat cepat dan relatif mudah dilakukan, menjadikannya metode populer dalam pemeriksaan las dan komponen struktural.
Keterbatasan MT adalah hanya dapat digunakan pada material ferromagnetik dan tidak efektif untuk mendeteksi cacat dalam pada material non-logam atau non-magnetik. Permukaan benda uji juga harus bersih dan rata agar hasil pengujian akurat.
Penetrant Testing (PT)
Penetrant Testing menggunakan cairan berwarna cerah atau fluoresen yang diaplikasikan ke permukaan benda uji. Cairan ini akan meresap ke dalam cacat permukaan seperti retakan halus, kemudian setelah dibersihkan dan diberi developer, cacat akan terlihat secara jelas.
PT cocok untuk berbagai jenis material seperti logam non-ferro, keramik, plastik, dan komposit. Teknik ini sangat sensitif terhadap cacat permukaan yang sangat kecil, bahkan tak kasat mata.
Meski mudah dan murah, PT hanya efektif untuk mendeteksi cacat terbuka di permukaan dan tidak bisa digunakan untuk mendeteksi cacat di bawah permukaan. Kebersihan permukaan sangat penting agar cairan penetran bisa meresap secara maksimal.
Eddy Current Testing (ET)
Eddy Current Testing memanfaatkan arus listrik bolak-balik yang menghasilkan medan elektromagnetik untuk mendeteksi cacat pada material konduktif. Arus pusar yang terbentuk akan terganggu jika ada cacat atau perubahan ketebalan material, dan gangguan ini diukur untuk dianalisis.
ET sangat sensitif terhadap cacat kecil di permukaan dan dapat dilakukan tanpa menyentuh langsung material, menjadikannya ideal untuk inspeksi cepat dan tanpa kontak. Metode ini banyak digunakan untuk memeriksa tabung logam, permukaan pesawat, dan komponen elektronik.
Namun, ET tidak dapat digunakan pada material non-konduktif dan memiliki keterbatasan kedalaman deteksi. Interpretasi hasil ET juga membutuhkan peralatan canggih dan tenaga ahli dengan pelatihan khusus.
Visual Testing (VT)
Visual Testing adalah metode paling dasar dalam NDT yang dilakukan dengan pemeriksaan langsung menggunakan mata atau alat bantu optik seperti kaca pembesar, endoskop, atau kamera. VT digunakan untuk mendeteksi cacat permukaan seperti retak, korosi, distorsi, atau cacat pada sambungan las.
Meskipun sederhana, VT sering menjadi tahap awal dalam inspeksi karena cepat, murah, dan tidak memerlukan peralatan kompleks. VT juga berguna untuk memverifikasi hasil dari metode NDT lainnya.
Akurasi VT sangat bergantung pada pencahayaan, keterampilan pengamat, serta kondisi permukaan material. Oleh karena itu, prosedur standar dan alat bantu sangat penting untuk memastikan konsistensi dan ketepatan hasil.
Aplikasi NDT di Berbagai Industri
Pengujian Non Destruktif digunakan secara luas dalam berbagai sektor industri karena kemampuannya mendeteksi cacat tanpa merusak benda uji. Setiap sektor memiliki kebutuhan spesifik terhadap teknik NDT yang berbeda, tergantung pada jenis material, lingkungan kerja, dan tingkat keselamatan yang dibutuhkan.
Industri Manufaktur
Dalam dunia manufaktur, NDT digunakan untuk memastikan bahwa produk akhir bebas dari cacat sebelum dipasarkan. Pemeriksaan ini dapat dilakukan pada komponen logam, plastik, atau komposit yang diproduksi secara massal, seperti alat berat, suku cadang mesin, dan produk elektronik.
NDT membantu produsen menjaga kualitas dan konsistensi produksi, menghindari cacat yang bisa menyebabkan keluhan pelanggan atau kegagalan fungsi. Teknik seperti UT, PT, dan VT sering digunakan dalam proses quality control dan inspeksi pasca-produksi.
Selain itu, penerapan NDT di lini produksi dapat meningkatkan efisiensi karena produk cacat dapat segera diidentifikasi tanpa menunggu proses perakitan selesai. Hal ini berkontribusi pada penghematan biaya dan peningkatan kepuasan pelanggan.
Industri Minyak dan Gas
Dalam sektor minyak dan gas, NDT memainkan peran krusial dalam menjaga keandalan sistem perpipaan, tangki penyimpanan, dan peralatan pengeboran. Karena lingkungan kerja yang ekstrem dan tekanan tinggi, deteksi dini terhadap cacat sangat penting untuk mencegah ledakan atau kebocoran.
Radiographic Testing (RT) dan Ultrasonic Testing (UT) sering digunakan untuk memeriksa sambungan las dan ketebalan pipa. Selain itu, Eddy Current Testing (ET) dapat digunakan untuk memantau korosi pada tabung atau peralatan berbahan logam konduktif.
NDT juga menjadi bagian dari pemeliharaan rutin (preventive maintenance) yang bertujuan mengurangi waktu henti operasional dan meningkatkan keselamatan kerja. Proses inspeksi ini biasanya dilakukan oleh tenaga bersertifikat sesuai standar keselamatan internasional.
Industri Penerbangan
Industri penerbangan memiliki standar keselamatan yang sangat ketat, sehingga NDT menjadi bagian wajib dalam perawatan dan inspeksi pesawat. Setiap bagian pesawat, mulai dari badan, sayap, hingga mesin, diperiksa secara rutin untuk mendeteksi keretakan mikro atau cacat struktural.
Metode seperti Magnetic Particle Testing (MT), Penetrant Testing (PT), dan ET banyak digunakan untuk memeriksa komponen logam pesawat. Visual Testing (VT) juga menjadi prosedur awal untuk menemukan tanda-tanda kerusakan yang bisa berkembang menjadi masalah serius.
Penggunaan NDT memungkinkan maskapai atau produsen pesawat memastikan bahwa setiap unit layak terbang tanpa harus membongkar keseluruhan sistem. Dengan demikian, jadwal operasional tidak terganggu dan keselamatan penerbangan tetap terjaga.
Sektor Konstruksi dan Infrastruktur
Dalam konstruksi, NDT digunakan untuk menilai kekuatan struktur seperti jembatan, gedung, dan terowongan. Pemeriksaan ini mencakup inspeksi sambungan las, tiang pancang, dan material beton atau baja yang digunakan dalam proyek.
Ultrasonic dan Radiographic Testing sangat berguna untuk memeriksa sambungan kritis pada rangka baja. Untuk permukaan beton, teknik seperti impact-echo atau ground penetrating radar (GPR) dapat digunakan untuk mendeteksi retakan dalam.
Penerapan NDT dalam tahap konstruksi maupun inspeksi rutin membantu mencegah keruntuhan struktur akibat cacat tersembunyi. Hal ini meningkatkan kepercayaan terhadap kualitas dan keamanan bangunan jangka panjang.
Pembangkit Listrik dan Energi
Pembangkit listrik, baik berbasis fosil, nuklir, maupun energi terbarukan, memanfaatkan NDT untuk memantau kondisi peralatan vital seperti turbin, boiler, pipa tekanan tinggi, dan reaktor. Cacat pada komponen ini bisa berakibat fatal jika tidak terdeteksi lebih awal.
Teknik seperti UT, RT, dan ET umum digunakan dalam inspeksi pipa uap bertekanan dan sistem perpindahan panas. NDT juga penting dalam pemantauan keausan dan korosi akibat paparan suhu tinggi dan bahan kimia.
Dalam industri nuklir, setiap prosedur NDT dilakukan dengan standar keselamatan dan ketelitian tinggi. Dokumentasi hasil inspeksi menjadi bagian dari pengendalian mutu dan izin operasional jangka panjang.
Industri Otomotif
Di sektor otomotif, NDT digunakan untuk memeriksa komponen seperti poros engkol, blok mesin, sambungan las pada rangka mobil, dan komponen sistem pengereman. Pemeriksaan ini dilakukan sejak tahap produksi hingga saat kendaraan digunakan.
Penetrant dan Magnetic Particle Testing adalah metode yang sering digunakan untuk mendeteksi retak mikro pada komponen logam. Sementara itu, Visual Testing dimanfaatkan dalam pengecekan akhir dan inspeksi rutin.
Penerapan NDT membantu produsen mobil mempertahankan kualitas, mengurangi risiko penarikan produk (recall), serta meningkatkan kepercayaan konsumen. Dalam proses perawatan kendaraan, NDT juga mendukung deteksi kerusakan dini sebelum menyebabkan kerusakan yang lebih besar.
Keunggulan dan Kelebihan NDT
Pengujian Non Destruktif memiliki banyak keunggulan yang menjadikannya metode pilihan dalam inspeksi teknis. Teknik ini memungkinkan evaluasi menyeluruh terhadap kondisi suatu material atau struktur tanpa harus merusaknya, sehingga efisien dan hemat biaya. Berbagai kelebihan NDT memberikan nilai tambah dalam hal keselamatan, keandalan, dan efektivitas proses pemeliharaan di berbagai sektor industri.
Tidak Merusak Benda Uji
Keunggulan utama dari NDT adalah kemampuannya untuk mengevaluasi kondisi material tanpa menimbulkan kerusakan. Ini berarti bahwa komponen yang diuji dapat tetap digunakan setelah inspeksi, berbeda dengan pengujian destruktif yang mengakibatkan kerusakan permanen.
Manfaat ini sangat penting terutama untuk komponen mahal, langka, atau yang tidak mudah diganti. Dengan menggunakan NDT, perusahaan tidak perlu mengorbankan produk hanya untuk memastikan kualitasnya. Hal ini mengurangi limbah material dan meningkatkan efisiensi operasional.
Kemampuan untuk melakukan pengujian berulang pada benda uji yang sama juga menjadi nilai tambah, karena memungkinkan pemantauan kondisi material sepanjang siklus hidupnya. Komponen yang kritis dapat terus diawasi tanpa perlu dihentikan penggunaannya.
Mampu Deteksi Cacat Tersembunyi
NDT dapat mendeteksi berbagai jenis cacat yang tidak dapat dilihat oleh mata manusia. Cacat seperti retakan mikro di dalam logam, korosi di bawah permukaan, atau rongga tersembunyi dapat diidentifikasi dengan metode yang tepat, seperti UT, RT, atau ET.
Deteksi cacat tersembunyi ini sangat penting untuk menjaga keandalan sistem yang bekerja dalam kondisi ekstrem atau bertekanan tinggi. Tanpa pengujian yang mendalam, cacat tersebut bisa berkembang menjadi kegagalan fatal yang merugikan.
Selain itu, kemampuan untuk mengetahui lokasi, kedalaman, dan ukuran cacat memungkinkan pengambilan keputusan yang tepat dalam perawatan atau penggantian komponen, sehingga keselamatan tetap terjaga tanpa pemborosan sumber daya.
Informasi yang Akurat dan Detail
Teknik NDT mampu memberikan data yang sangat detail mengenai kondisi internal maupun eksternal suatu material. Informasi ini mencakup ukuran cacat, orientasi, bentuk, serta kedalamannya, tergantung pada metode yang digunakan.
Data yang diperoleh dapat didokumentasikan dalam bentuk grafis, digital, atau visual yang memudahkan proses pelaporan dan analisis. Teknologi canggih dalam peralatan NDT modern juga memungkinkan integrasi hasil dengan sistem manajemen pemeliharaan atau perangkat lunak simulasi teknik.
Akurasi informasi yang dihasilkan dari pengujian NDT membantu para insinyur dan teknisi dalam menyusun rencana tindakan yang tepat, baik untuk perbaikan segera maupun untuk perencanaan jangka panjang. Ini menjadikan NDT sebagai alat manajemen risiko yang sangat efektif.
Fleksibilitas Penggunaan di Berbagai Material
NDT dapat diaplikasikan pada berbagai jenis material, baik logam ferromagnetik, non-ferro, plastik, beton, maupun komposit. Setiap jenis material memiliki karakteristik berbeda yang dapat diperiksa dengan teknik tertentu yang sesuai.
Fleksibilitas ini membuat NDT sangat berguna dalam berbagai aplikasi industri, dari manufaktur hingga energi, dari otomotif hingga infrastruktur. Tidak hanya digunakan untuk produk akhir, NDT juga bisa diterapkan dalam tahap pengembangan produk, produksi massal, hingga inspeksi pasca-pemasangan.
Selain itu, teknik NDT juga dapat disesuaikan dengan berbagai bentuk dan ukuran komponen, mulai dari tabung sempit hingga struktur berskala besar. Alat bantu portabel maupun sistem otomatisasi juga semakin memperluas ruang lingkup penggunaan NDT dalam kondisi lapangan maupun di laboratorium.
PJK3
PJK3 adalah singkatan dari Perusahaan Jasa Keselamatan dan Kesehatan Kerja yang ditunjuk oleh Kementerian Ketenagakerjaan untuk melaksanakan layanan teknis di bidang K3. Dalam konteks pengujian non-destruktif seperti ultrasonic test, keberadaan PJK3 sangat penting guna menjamin bahwa proses pemeriksaan dilakukan sesuai standar keselamatan kerja yang berlaku di Indonesia.
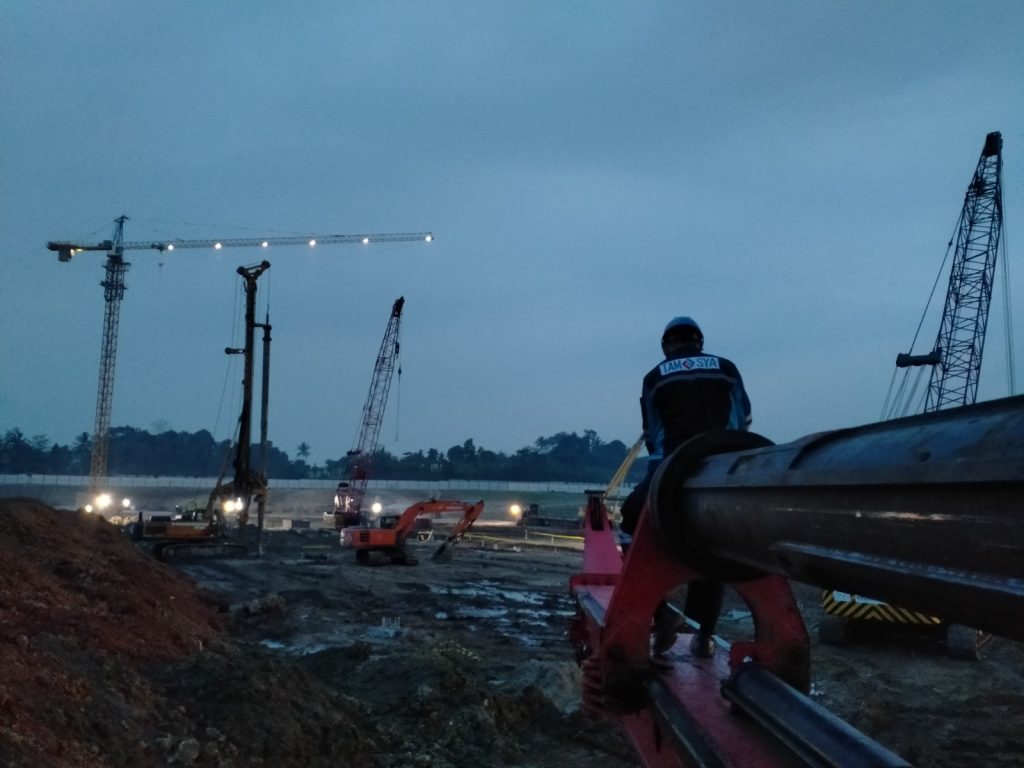
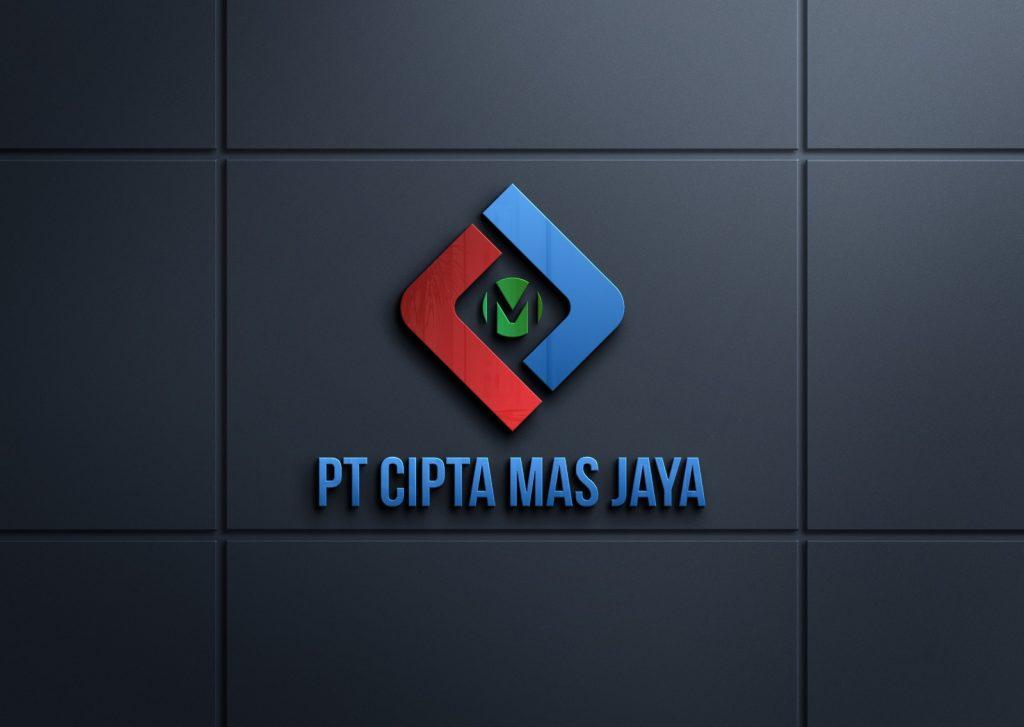
PJK3 Riksa Uji
PJK3 Riksa Uji adalah perusahaan yang secara khusus diberi kewenangan oleh pemerintah untuk melakukan kegiatan inspeksi, pemeriksaan, dan pengujian terhadap peralatan kerja dan fasilitas industri. Salah satu cakupan tugasnya adalah melakukan uji tidak merusak (NDT), termasuk ultrasonic testing, demi memastikan kelayakan dan keamanan alat produksi.
PJK3 Riksa Uji wajib memiliki tenaga ahli bersertifikat dan peralatan pengujian yang memenuhi standar nasional maupun internasional. Mereka juga harus menerapkan sistem mutu dan prosedur kerja yang diakui, seperti mengikuti ketentuan Permenaker dan standar teknis lainnya.
Peran PJK3 sangat vital karena hasil pengujian mereka menjadi dasar pengambilan keputusan teknis terkait operasi dan perawatan alat produksi. Oleh karena itu, memilih PJK3 yang kompeten dan terpercaya sangat menentukan kualitas dan legalitas hasil pemeriksaan.
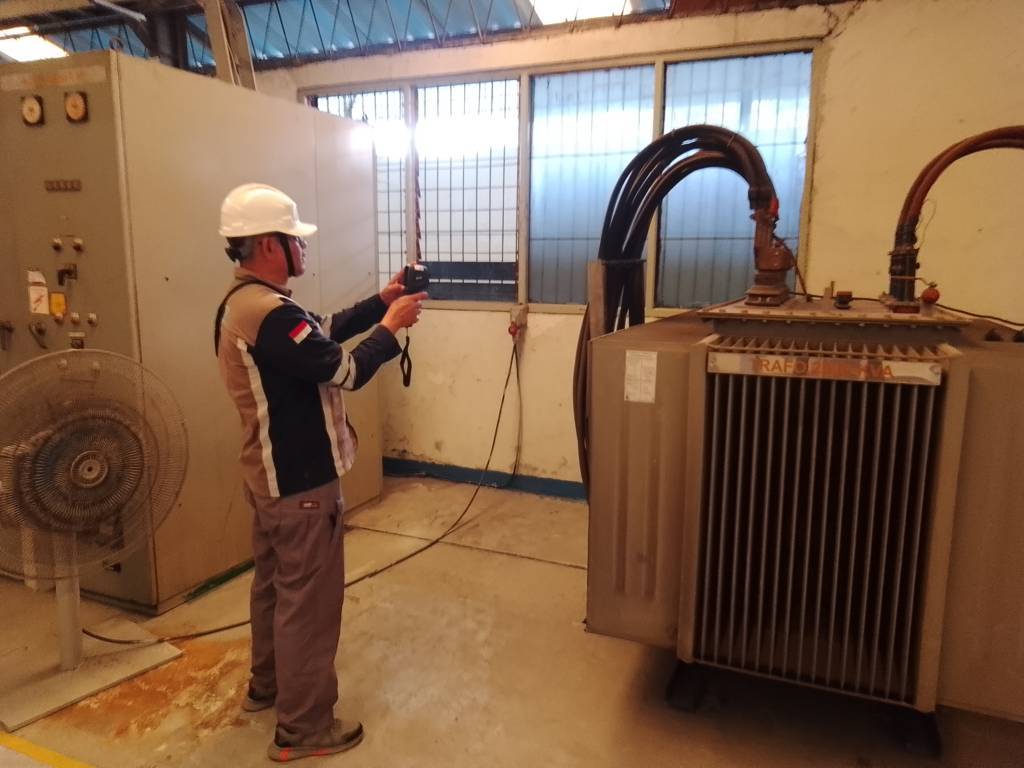
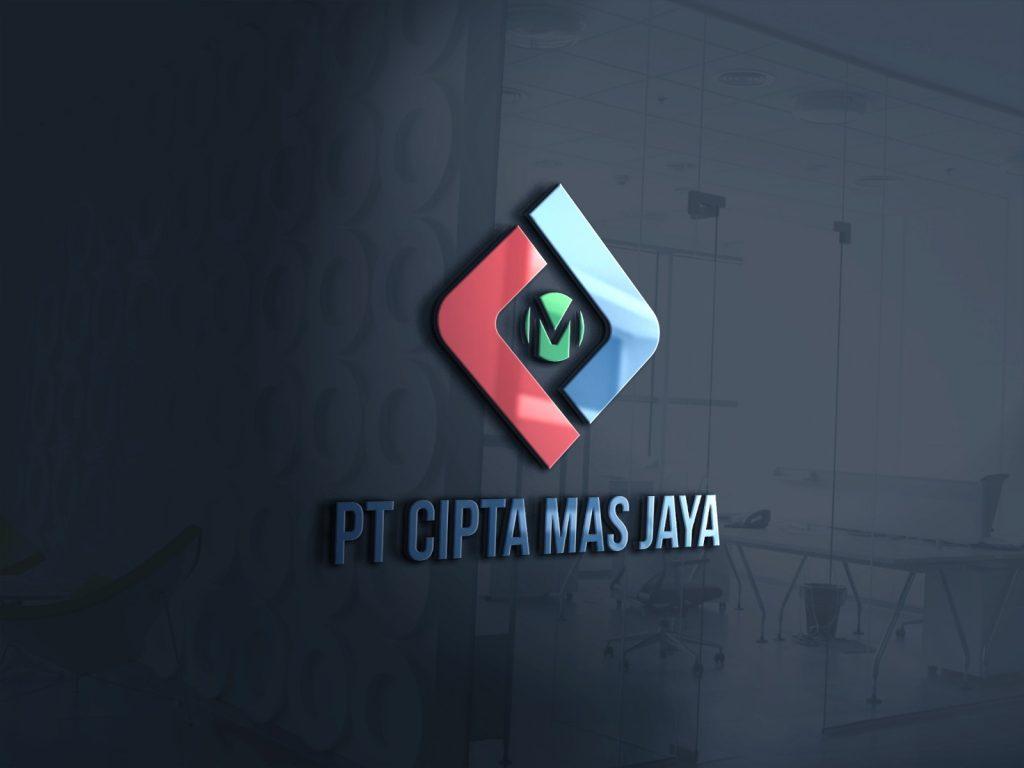
PT. Cipta Mas Jaya adalah PJK3 Riksa Uji
PT. Cipta Mas Jaya adalah salah satu perusahaan yang telah ditunjuk sebagai PJK3 Riksa Uji oleh Kementerian Ketenagakerjaan RI. Perusahaan ini memiliki izin resmi dan tenaga kerja kompeten dalam melakukan pengujian, khususnya di bidang inspeksi peralatan dan pengujian non-destruktif seperti ultrasonic testing.
Sebagai PJK3 Riksa Uji, PT. Cipta Mas Jaya telah berpengalaman menangani berbagai sektor industri, mulai dari manufaktur, energi, migas, hingga konstruksi. Komitmen perusahaan dalam menjaga standar mutu dan keselamatan menjadikannya mitra terpercaya dalam memastikan peralatan kerja layak dan aman digunakan.
Legalitas sebagai PJK3 memberi jaminan bahwa setiap layanan yang diberikan PT. Cipta Mas Jaya mengikuti prosedur sah dan hasilnya dapat dipertanggungjawabkan di hadapan regulator maupun auditor.
PT. Cipta Mas Jaya Melayani Jasa Pengujian Non-Destruktif
PT. Cipta Mas Jaya tidak hanya melayani jasa riksa uji pada peralatan kerja, tetapi juga menyediakan layanan pengujian non-destruktif (NDT), termasuk ultrasonic testing, magnetic particle testing, penetrant testing, dan radiography. Layanan ini dirancang untuk mendeteksi kerusakan atau cacat pada peralatan industri tanpa merusak struktur aslinya.
Dengan dukungan alat uji modern dan teknisi bersertifikat, PT. Cipta Mas Jaya mampu memberikan hasil pengujian yang akurat, cepat, dan sesuai standar. Setiap proses dilakukan dengan dokumentasi lengkap dan pelaporan yang transparan, sehingga klien mendapatkan informasi teknis yang dapat dijadikan dasar pengambilan keputusan.
PT. Cipta Mas Jaya juga melayani konsultasi terkait riksa uji k3 pengujian dan pengawasan teknis, menjadikannya solusi menyeluruh dalam bidang K3 teknis dan pengujian non-destruktif. Bagi perusahaan yang membutuhkan layanan pengujian terpercaya dan sah secara hukum, PT. Cipta Mas Jaya adalah pilihan yang tepat.
Artikel Terkait:
NDT Ultrasonic Testing adalah
NDT Ultrasonic Testing adalah salah satu metode pengujian non-destruktif (Non-Destructive Testing) yang digunakan untuk mendeteksi cacat atau ketidaksempurnaan di dalam...
Prinsip Kerja Belt Conveyor
Prinsip Kerja Belt Conveyor adalah cara kerja sistem sabuk berjalan yang digunakan untuk memindahkan material dari satu titik ke titik...
Fungsi Belt Conveyor
Fungsi Belt Conveyor adalah mengangkut material dari satu lokasi ke lokasi lain dalam proses produksi maupun distribusi secara efisien. Peralatan...
Jenis – jenis Belt Conveyor
Belt conveyor atau sabuk konveyor memiliki beberapa jenis yang berbeda, tergantung pada material sabuk dan desainnya. Beberapa jenis utama meliputi...
Faktor-faktor Lingkungan Kerja K3
Faktor-faktor lingkungan kerja K3 meliputi faktor fisik, kimia, biologi, ergonomi, dan psikososial. Faktor fisik seperti suhu, kebisingan, getaran, dan pencahayaan...
Artikel Yang Diperbarui:
Konsultan Uji Riksa
Konsultan Uji Riksa adalah pihak atau badan usaha yang memiliki keahlian teknis, legalitas resmi, serta kewenangan untuk melakukan pemeriksaan (riksa)...
Keunggulan Forklift Elektrik
Keunggulan forklift elektrik adalah kemampuannya untuk memberikan operasi yang lebih ramah lingkungan tanpa menghasilkan emisi gas buang, sekaligus menawarkan biaya...
Pengujian Penetran (Penetrant Testing)
Pengujian Penetran (Penetrant Testing), atau biasa dikenal sebagai Dye Penetrant Testing (DPT), adalah metode pemeriksaan non-destruktif yang digunakan untuk mengidentifikasi...
Riksa Uji Grounding System
Riksa uji grounding system atau sistem pembumian penangkal petir sangat berkaitan erat dengan riksa uji penyalur petir karena keduanya bekerja...
Uji Beban Kantung Air (Water Bag Load Test)
Uji Beban Kantung Air atau Water Bag Load Test adalah metode pengujian beban yang menggunakan kantong berisi air sebagai media...